Главная
Гостевая
Фото
Акустический тюнинг
Внешний тюнинг
Тюнинг двигателя
Тюнинг подвески
Тюнинг салона
Тюнинг тормозов
Тюнинг трансмиссии
Тюнинг
электрооборудования
|
Акустическая система
Интерес к самодельным компонентам
вызван тем, что при создании качественной автомобильной установки
обойтись только готовыми изделиями практически невозможно. В последние
годы в радиолюбительской литературе появилось немало публикаций,
посвященных самостоятельному изготовлению автомобильной аудиотехники,
главным образом усилителей.
Но источник сигнала и усилитель - только надводная часть целого
айсберга проблем, встающих перед создателем автомобильной установки.
Огромное влияние на качество звучания оказывает конструкция акустической
системы, причем это влияние намного больше, чем в "домашних" системах.
Однако этот факт еще не стал очевидным и многие автолюбители пытаются
улучшить качество звучания простой заменой динамиков и магнитол, хотя
проблема вовсе не в этом.
Скептическое отношение к Hi-Fi в автомобиле вызвано прежде всего
безграмотным подходом к установке акустических систем. Самая
распространённая ошибка - установка мощных и высококачественных
динамиков на задней полке, а спереди - что придется, или вообще ничего.
Видимо, владелец на концерте предпочитает сидеть спиной к сцене...
К сожалению, радиолюбители только недавно стали уделять внимание
созданию высококачественных акустических систем для автомобиля. Основная
проблема - воспроизведение низкочастотной части звукового диапазона.
Далее приводится описание очень удачной конструкции низкочастотной
акустической системы для размещения под передними сиденьями ВАЗ-2108 и
2109. Подобные методы можно использовать для создания акустических
систем в автомобилях других марок. В конструкции использованы доступные
и недорогие материалы.
Попытки получить достойные "басы" в салоне автомобиля
предпринимались с момента зарождения автозвука. До наступления "эры
сабвуферов" для размещения басовых динамиков использовалась задняя полка.
Несколько позже, когда до сознания масс дошло, что звук должен исходить
спереди, стали использовать передние двери, штатные места в торпедо,
кикпанели. И тут начались проблемы. Основное условие качественного
звучания создание оптимального акустического оформления для конкретных
динамических головок. Для воспроизведения низкочастотного диапазона
необходимо выдержать оптимальный объем корпуса. При его уменьшении
относительно оптимума воспроизведение низких частот будет ослаблено. От
увеличения объема пользы еще меньше колебания диффузора не будут
демпфированы в нужной степени. В результате воспроизведение низших
частот будет сопровождаться гулким призвуком, а при некоторой "настойчивости"
можно оборвать подвес диффузора или выводы звуковой катушки даже при
скромной подводимой мощности. Кикпанели и торпедо для низкочастотного
оформления обычно непригодны. Поэтому при построении многополосных
систем в автомобиле головки чаще всего располагают в передних дверях. Во
многих случаях это оправдано, так как большинство автомобильных головок
рассчитано именно на такое акустическое оформление. Однако установка в
двери имеет ряд недостатков. Трудно обеспечить требуемый объем для
головок, предназначенных для установки в такие виды акустического
оформления, как закрытый ящик или фазоинвертор, добиться герметичности
еще сложнее. Необходимо провести тщательное вибродемпфирование и
шумоизоляцию панелей и механизмов двери, иначе она будет "подпевать" уже
на средней громкости. Да и динамики нужны влагостойкие.
Альтернативный вариант, лишенный этих недостатков акустические
системы под передними сидениями. Идея не новая, двух, трех- и даже
четырехполосные автомобильные акустические системы "почти как дома" были
очень популярны в первой половине восьмидесятых. В пору расцвета это
были добротные изделия с жесткими корпусами, хорошими разделительными
фильтрами и продуманным креплением. Готовые корпусные колонки неплохо
вписывались в интерьер автомобиля и устанавливались без проблем.
Довольно быстро они "ушли" с задней полки и заняли место под передними
сиденьями, где уже не так бросались в глаза недоброжелателям. Между
делом обнаружилось, что звучание от "переезда" только выиграло. Но как
только производители автомобилей уделили внимание штатным местам,
позиции корпусной акустики пошатнулись, а с появлением сабвуферов она и
вовсе сошла со сцены. Тонкостенные коробочки с крошечными динамиками,
появляющиеся иногда в продаже всего лишь тень былой роскоши.
Диалектика учит нас, что развитие идет по спирали. Поэтому возобновление
интереса к акустическим системам под передними сидениями закономерно
это позволяет относительно простыми средствами решить проблему "переднего
баса". Идея использовать ящики под сидениями как вариант акустического
оформления низкочастотного звена в многополосной системе была навеяна
действующими образцами в автомобилях ВАЗ-2107 и "Москвич-2141".
Воспроизведение частот от 40 50 Гц и звуковое давление этих систем
произвели сильное впечатление. Размещение ящиков под сидениями поначалу
казалось делом несложным. Но, заглянув в то место салона "зубилы", где в
дальнейшем предстояло стоять ящикам, я был немного ошарашен. Это была не
"классика", с которой произошло первое знакомство. Установленные мной
для себя требования "технического задания" состояли из трех пунктов:
выжать максимально возможный объем, не нарушить функциональность сидений,
обеспечить легкость монтажа (правда не в смысле облегчения демонтажа
злоумышленнику). Идея установки динамика показана на рис. 1.
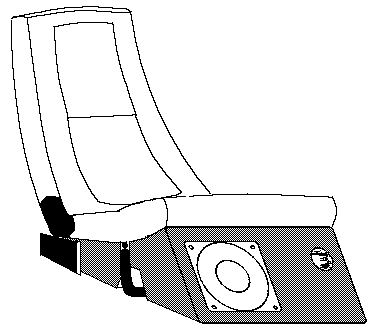
Рис. 1. Установка динамика под сидением
автомобиля.
Каждый,
заглянувший под сидение, видел, какой небольшой проем образован дугой
передней опоры и каркасом. Поэтому решение заключалось в том, чтобы
сделать переднюю опору разборной. Для этого было снято сидение, затем
срублены заклепки, которые соединяют дугу с каркасом. По размерам этих
заклепок изготовлены болты (рис. 2), все шейки которых взяты с заклепок.
Только на конце резьба добавилась.
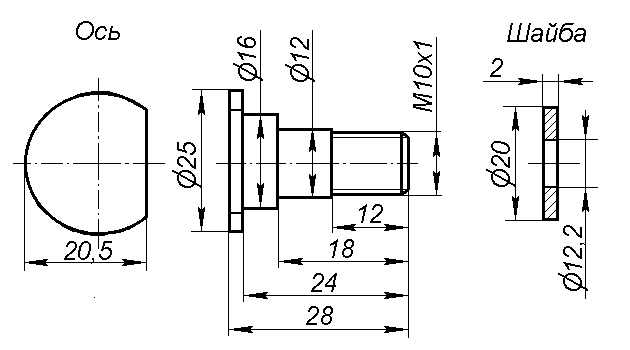
Рис. 2. Конструкция крепежных болтов.
Это хозяйство облегчило в дальнейшем
проектирование ящика. Скажу сразу, все проектировалось на месте, без
каких либо предварительных промеров, только путем проведения постоянных
прикидок. Для этого понадобился гофрокартон, ножницы и скотч.
Предварительно сидение было установлено на 4 болта салазок и откинуто к
подушке заднего сидения. Дуга передней опоры с пружинами тоже была
прикручена к полу, как положено. Болты, соединяющие все части сидения в
одно целое, лежали рядом. Из картона я вырезал полосу такой ширины,
чтобы она с минимальными зазорами разместилась между стойками дуги.
Затем выгнул профиль, с минимальными зазорами огибающий крепления дуги.
Потом уже подобрал приблизительно длины передней (до крепления) и задней
частей ящика.
Следующим шагом было изготовление боковых стенок. Это не составило
особого труда, я просто опускал сидение, смотрел, поднимал, подрезал
лишнее и снова опускал. Самым быстрым способом соединения частей макета
я посчитал соединение с использованием скотча. Потом была сделана
верхняя часть макета. Сидение опущено, собранно на болты, и вот вроде
результат. Есть все необходимые размеры. Но как я тогда ошибался!
По снятым размерам из 12- миллиметровой фанеры были изготовлены все
части будущего ящика, за исключением фрагмента, огибающего крепление
передней опоры. Этот фрагмент был изготовлен по композитной технологии.
Стеклоткань по торцам боковых сторон и дна ящика была подклеена, а затем
пропитана эпоксидной смолой и упрочнена еще несколькими слоями кусочков
стеклоткани.
Когда все было собрано, пришло первое разочарование. Ящик уместился
на своем месте прекрасно, но вот сидение вставать не хотело. Анализ
показал, что промахнулся я с размерами боковых стенок и с использованием
в качестве материала для макета гофрокартона. Каркас сидения имеет
выгнутый профиль. При "примерках" он прогибал гофрокартон. А так как для
того чтобы прогнуть его, особых усилий не требовалось, я этот подвох не
заметил.
Лимитирующей позицией пока оставалась высота боковых стенок.
Постепенно уменьшая ее и проводя постоянные прикидки, я добился
максимального использования пространства. Хочу добавить, что я
прикидывал взаимное расположение ящика и сидения, передвигая последнее
из одного крайнего положения в другое. На этом этапе, возможно, придется
уменьшить длину задней части, если вдруг в ящик начнет упираться пруток
фиксатора промежуточных положений сидения.
Теперь ограничением стала выступать верхняя часть ящика. При
использовании фанеры я опять натыкался на то, что выпуклая часть каркаса
сидения упиралась в фанеру. Снижать высоту - значит уменьшать объем
ящика, который по прикидкам получался около 8 литров. Опять
проанализировав ситуацию, пришел к тому, что верх надо изготавливать
также по композитной технологии. При очередной прикидке объекта "на
местности", замерил расстояние от выпуклой части каркаса сидения до
боковых стенок ящика. Потом на чуть меньшем расстоянии от боковых стенок
в ящике были установлены дополнительные перегородки, расположенные под
небольшим углом к боковым и имеющие меньшую высоту, так что при
очередных прикидках расстояние между каркасом сидения и ребрами было
порядка 10 мм. Для них предназначалась роль не только ребер жесткости,
но и линий преломления стеклоткани при формировании верха ящика. От
боковых стенок стеклоткань резко спадала вниз до ребер. А между ними
имела небольшой, специально созданный прогиб. Ребра расположились только
до изгиба нижней плоскости ящика (рис. 3).
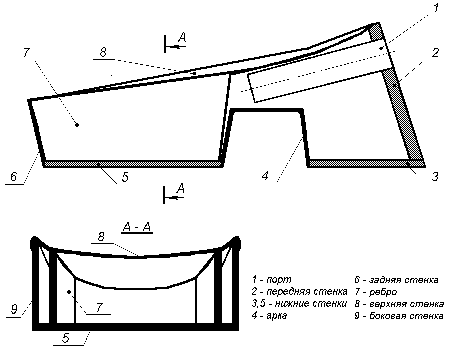
Рис. 3. Конструкция корпуса.
Дальше ткань просто равномерно натянул.
Перед пропиткой эпоксидной смолой можно провести еще одну прикидку. Я от
нее отказался, так был полностью уверен в успехе. Фронтальный срез ящика
я укрепил рамкой из брусков. К верхнему бруску была приклеена
стеклоткань. Затем жесткость верхней панели была доведена до приемлемой
путем наклеивания еще нескольких слоев стеклоткани. Причем последующие
слои были сделаны с напуском на боковые стороны и приклеены к боковым
стенкам под грузом. Замечу, что задняя, совсем узкая стенка была
выклеена заодно с верхней. После того, как просохла смола, я произвел
вибродемпфирование путем наклеивания визомата на поверхность фанеры.
Стеклотканевую поверхность вибродемпфировал резинобитумной мастикой.
Осталось изготовить фронтальную панель, на которой должна будет
разместиться головка. Я изготовил ее из двух слоев фанеры, склеенных
клеем ПВА и дополнительно стянутых шурупами. Отверстие под головку
вырезал на токарном станке. Как я раньше упоминал, в первом варианте
решил использовать 6-дюймовые мидбасы. По периметру панели снял фаску
достаточно больших размеров. Потом, приложив панель к ящику, приклеил ее,
заполнив полость, образованную торцами стенок ящика и фаской панели,
смесью мелких опилок и клея ПВА. Прочность получилась достаточной, так
как при переходе к второму варианту пришлось потрудиться стамеской,
расшивая проклеенные поверхности.
Что же в итоге получилось? Ящик при определенной сноровке
устанавливается минут за пятнадцать. Основная проблема - на ощупь
завести болты соединения передней опоры и сидения. Я был готов потратить
на это дело и час, так как устанавливаются ящики один раз и надолго.
Встают достаточно плотно. Никаких дополнительных креплений не
применялось. Сидения свободно перемещаются между крайними положениями.
Измеренный объем ящиков составил 7,5 литров. Много это или мало? Для
6 дюймовых Macrom оказалось: очень мало. Как выход из тупика пришла
мысль: из задней стенки сделать панель акустического сопротивления. Но
до опытов дело не дошло. Решение было принято такое: применить динамик
25ГДН34. Произведены необходимые расчеты для салона автомобиля с
использованием программы JBL Speaker Shop. Наилучшее акустическое
оформление для этих головок фазоинвертор объемом 7,5 литров с
настройкой на частоту 50 Гц. В моей аудиосистеме изначально
предполагалось использовать сабвуферы, поэтому и была выбрана эта
частота. Хотя, если использование сабвуферов не предполагается, частоту
настройки можно взять ниже, реально до 40 Гц.
В итоге был получен тот результат, на который и рассчитывал. Во
первых, удалось разместить "под седлами" ящики минимально приемлемого и
максимально возможного в этом случае объема. Во вторых, это никак не
сказалось на функциональности сидений. В третьих, есть перспективы на
базе этих ящиков сделать более мощную акустическую систему, применив,
например, головки Rocford Fosgate.
Эскизы основных деталей приведены на рис. 4
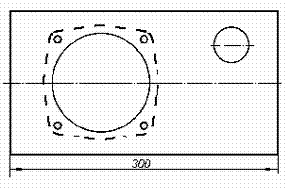

Рис. 4. Эскизы основных деталей
крепления.
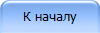
Сразу
оговорюсь - все картинки можно открыть для просмотра в большом виде если
по ним щелкнуть.
Материал и инструменты: Вариант
полностью делать из монтажной пены меня не устраивал, т.к. для этого
нужна еще стеклоткань, эпоксидка, ехать специально в магазин за
стеклотканью у меня не было времени, к тому же эпоксидка и пена очень
сильно пачкаются, хотелось сделать из того, что было под руками. Решил
все сделать
из 2см ДСП. Нам понадобится ДСП, клей ПВА, клей для дерева (фото 1 и 2)
или аналог, автомобильная шпаклевка (можно обойтись только напильником),
материал которым будем обтягивать, а также электролобзик, саморезы,
крупная шкурка и напильник.
 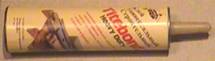
Для начала снял обшивку,
принес её домой и сделал шаблоны из картонной коробки. (фото 3,4 и 5).
По моему замыслу должно было получится три слоя ДСП, т.е. 6 см в глубину
+ 2 см от обшивки двери до металла (под обшивкой) итого 8 см, этого
достаточно для нормального динамика, чтобы он не уперался в металл
магнитом, если этого не хватит лучше резать металл, чем добавлять еще
один слой ДСП (будет мешать ногам). Штатная дырка под обшивкой довольно
небольшого диаметра, у меня туда не встал 25 ГДШ 13см, не пролез магнит.
Получилось 3 детали.

Выпилил по шаблонам все детали. (фото 6,7 и 8). Далее при помощи клея
ПВА и саморезов я собрал два подиума, дал им просохнуть, напильником
подравнял все неровности, и зашпаклевал торцы и шляпки саморезов (для
этого можно использовать и смесь ПВА с опилками).
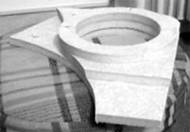
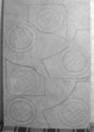
Пришло время для соединения подиума со
штатным карманом двери, для этого отрезал часть кармана, чтобы карман
был впритык к подиуму. (рисунок 9) и приложив к обшивке прикрутил 3-мя
саморезами.
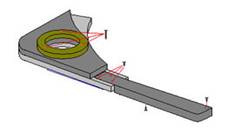
Совсем впритык к подиуму не получается, карман
срезается не заподлицо, т.е. между частью кармана, которая прилегает к
подиуму и 1-ым слоем подиума остается небольшой промежуток в 3 мм.
Теперь я залил этот стык монтажной пеной (фото 10 и 11). Обрезал ножом
лишку и зашкурил, шкурится просто потрясающе, можно придать любую форму.
Зашпаклевал пену и зашкурил. (фото 12, 13 и 14)
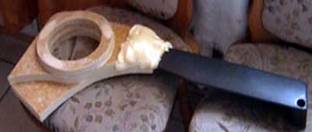
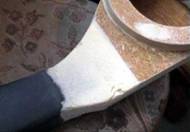
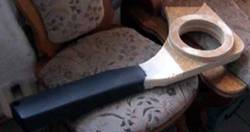
Отделка:
изначально я хотел все это покрасить черным антигравием - покрасил,
получился довольно отвратительный вид. Я думал, что антигравий своим
слоем скроет шершавость ДСП и стыков, но он наоборот только подчеркнул,
как обычная краска (если все же кто-то хочет покрасить, то Вам придется
шпаклевать и шкурить весь подиум именно под покраску, а это довольно
сложно и муторно). Тут настроение моё упало, стал пробовать обтягивать
дермонтином, но он не захотел этого даже с феном и зажигалкой, я
растроился и пошел спать. На следующее утро пришла идея обтянуть
материалом от пальто (не помню как называется). При помощи клея для
дерева (фото 6) мне это удалось. Материал
довольно хорошо растягивается и одним куском я обтянул весь подиум Я
использовал клей с фото 1, очень рекомендую этот клей, он остается
упругим после засыхания (не крошется), встает в течении 3-5 минут.
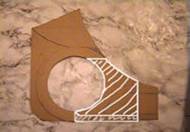
Приложил мое произведение к обшивке и стал думать как
смастерить подпятник. Подпятник нужен для того, чтобы закрыть щель
между вдавленностью на двери (рисунок 15) и плоскостью подиума. (изображен
синим цветом на рисунке 9). Тогда я сделал два подпятника из оргалита,
2-й просто чуть длинней. (фото 16) и приклеил их к подиуму. Не срезайте
сразу материал на подиуме заподлицо, оставьте на подпятник.
Затем я прорезал ножом дырку в обшивке и прикрутил подиум на 7-ми
саморезах + 1 штатный саморез в карман с внутренней стороны + винт с
внешней стороны, когда вешаешь на дверь. Вот что из этого получилось:
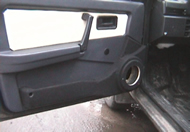
Единственное, что стоило бы еще сделать так это
придать направленность динамическим головкам. Аккуратненько ножовкой по
металлу срезать последнее кольцо из ДСП по диагонали, но при этом надо
учитывать, что магнит может упереться в стенки колодца, так что
внутренний диаметр нужно выбрать несколько больше.
На
фотографиях в подиумах временно установленны 13 см динамики 25 ГДШ через
проставки (тоже обтянуты материалом). После подключения динамиков (они
были переставлены из штатных мест) звук изменился довольно сильно в
лучшую сторону, динамики действительно заиграли, появились хорошие
средние частоты (почти мидбасс), в штатные места я поставил 10 см
динамики все динамики были разделены самодельными фильтрами (как модно
говорить кроссоверами). В общем я, скажу прямо, неожидал таких улучшений,
посмотрим, что будет когда поставлю компонентную 16,5 см акустику. В
итоге я потратился только на антигравий, который мне оказался не нужным,
всё остальное у меня было.
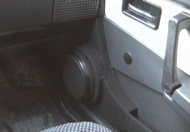
Это сама головка 25 ГДШ, довольно
увесистая. Не каждый 16 см динамик имеет такую магнитную систему. Справа
грили 16,5 см от Infinity 655cs, которые у меня стоят в Акценте и 13 см
от JVC, которые ушли вместе с моей предыдущей машиной.
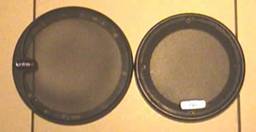
Источник:
http://www.td-audio.ru/tuxamat
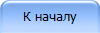
Автор - Черепанов Антон Сергеевич
Известно, что ни одна серьезная установка не обходится без подиумов под
передние мидбасы. Причем практически в любой модели автомобиля. Поэтому
передо мной не стоял вопрос "делать - не делать", а оставалось лишь
определиться с конструкцией.
Пару слов о построении системы. Впереди я планировал применить
трехкомпонентную схему:
мидбас 16 см -- на подиумах в дверях
мидренж 13 см - в штатных местах (высокая панель)
пищалки - на передних стойках.
Об ориентации мидбасов. По правильному углы установки динамиков нужно
подбирать долго и упорно, экспериментальным путем. Но делать призовую
установку я не собирался, а "вырулить" сцену намеревался в дальнейшем с
помощью мидренжа и пищалок, что вполне допустимо. Поэтому форма и угол
наклона были выбраны на глазок.
Идея обтягивать трикотажной майкой фанерный каркас мне не приглянулась,
просто напылять макрофлекс на обшивку -- тоже не вариант, поэтому выбрал
промежуточную схему: на силовой деревянный каркас напыляется макрофлекс
и оклеивается стеклотканью.
Основные материалы:
Фанера 8 мм, приблизительно 0,8 кв.м.,
обрезки оргалита и толстого картона.
Стеклоткань толщиной 0,25 мм,
куплена в магазине для авиамоделистов, порядка 2 кв.м. Также прикупил и
ткань 0,06 и углеленту, но они мне как-то не пригодились...
Эпоксидный клей ЭДП, использовал
упаковку по 150 гр., очень удобно -- разводил сразу весь флакон. Расход
составил 6-7 упаковок. Производство г. Воронеж
Полиэстерная шпаклевка со
стекловолокном "???", одна баночка 250 гр, стоила порядка 100 руб.
Шкурка, резиновый держатель для
шкурки (продается на всех строительных рынках, очень удобный!), резак,
клей ПВА, пластилин, Макрофлекс (одного баллона хватит), саморезы,
маленькие гвоздики.
Начал с примерки: после двух макетов из бумаги стало совершенно ясно,
что приемлемая форма нижней части может быть только одна. Поэтому я из
8-мм фанеры вырезал дно подиума, кольцо под динамик и боковые распорки.
Кстати замечу, что все детали я вырезал сразу в двойном экземпляре - так
гораздо проще их подгонять, да и при шлифовке проще соблюдать прямые
углы.
Собрал силовую конструкцию при помощи ПВА и гвоздиков 20мм. Она и сама
по себе оказалась довольно прочной...
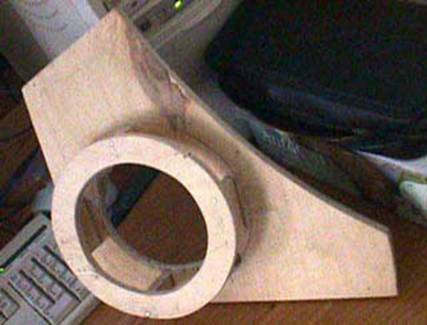
Внутренний диаметр кольца взрезан с
запасом, внешний же выбран почти вровень с головкой - 175 мм.
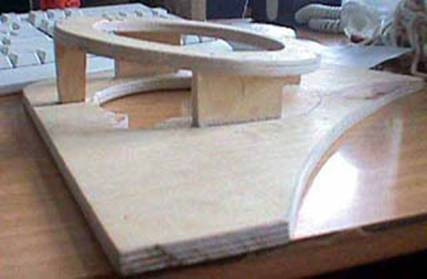
На переднем плане виден вырез под
выступающую часть штатного кармана.
Теперь про карман двери. Я сразу
отказался от затеи делать его заново из фанеры - штатный пластиковый
вполне хорош. Поэтому отвинтил его от обшивки и подпилил таким образом,
чтобы он ровно прилегал к основанию подиума.
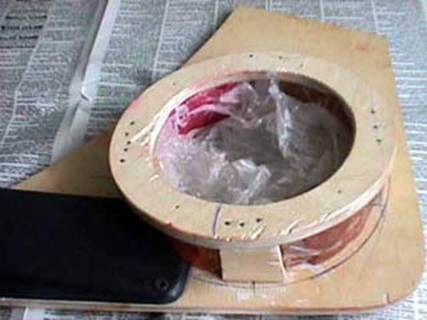
Видно как подпилена передняя часть
кармана.Пластилин предварительно завернут в целлофан, чтобы потом легче
было его вытащить из макрофлекса.
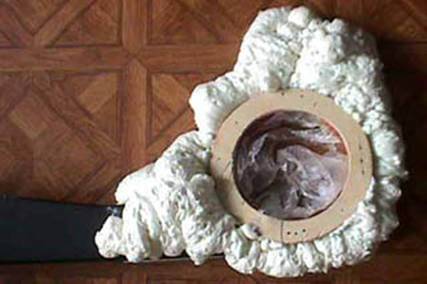
Заливка в два захода
Готовую конструкцию залил Макрофлексом. Накладывать надо тонким слоем,
толстый плохо сохнет, особенно внутри. Излишки подрезал ножом, требуемую
форму придал с помощью крупнозернистой шкурки.
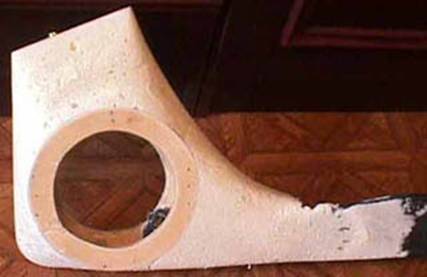
Практически готово под оклейку стеклотканью.Крупные
раковины и дыры заполнил ЭДП с опилками.
Не всегда получается придать желаемую форму макрофлексу - внутри он
довольно мягкий. Поэтому можно перед оклейкой подшпаклевать поверхность.
Фронтальная акустика: подиумы
Использовал толстую стеклоткань (СТ) - 0.25 мм. СТ пропитана парафином,
пришлось предварительно прокаливать ее на огне. Можно это делать и в
духовке, но я не советую :-)
Предварительно втерев эпоксидку в пену, аккуратно накладывал СТ, также
пропитанную смолой. Форма болванки позволяла уложить один цельный кусок
СТ без перегибов и надрезов. Свисающие излишки подгибал, иногда
прихватывал гвоздиками к фанерному основанию. Слои почти не шлифовал.
В общей сложности положил три слоя СТ толщины 0,25, конструкция
получилась прочная. Счел излишним оклеивать углелентой, подиум и так
выглядел как каменный - сказался силовой каркас. Хотя для бОльшей
прочности можно было все-таки дать пару слоев углеволокна :-)

Оклеенные и зашпаклеванные подиумы. Готовы к
окончательной отделке
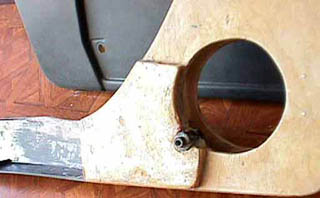
На переднем плане - "задник".Слева видно, как СТ
захлестывает пластик кармана, обеспечивая жесткость переходу
Чтобы подиум прилегал к обшивке по
всей площади основания, пришлось вырезать из оргалита дополнительный "
задник". Приклеил его к фанере эпоксидкой, требуемую толщину подбирал
кусочками картона уже по месту.
Шпаклевку накладывал пластиковым шпателем, ложится неплохо, только очень
маленькое время жизни у приготовленной порции - несколько минут. Зато
быстро застывает, пока один подиум намажешь, другой уже высохнет. Как
видно из фото, форма получилась довольно ровная - много шпаклевать не
пришлось. Основное внимание уделил стыку кармана и подиума.
Выравнивал шкуркой средней зернистости, делал все на балконе - сильно
летит стекловолокно наполнителя, от него потом все чешется :-) Работал в
резиновых перчатках.
Предварительно подиумы вместе с карманом выкрашены черной матовой
нитрокраской. Смотрится вполне достойно, хотя поверхность подготовлена
явно не под покраску.
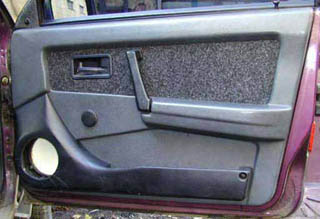
Покрасил в один слой только для вида.Нижнее
углубление в обшивке тоже будет оклеено ковролином. Но позже...
В дальнейшем планирую обтянуть подиумы винилом. Винил уже куплен, он т.н.
"мебельный", вроде как соответствует понятию "4-way" (тянется в четыре
направления). Был найден на строительном рынке. Стоит недорого. Таким
винилом я уже обтягивал один подиум (не этот!), правда более рельефной
формы - результаты более чем приемлемые.
При обтяжке использовал клей БФ-88
и строительный фен. Клеем намазывал обе поверхности, концентрическими
кругами от посадочного места под динамик, винил несильно грел феном и
без особых усилий укладывал. Все сразу мазать не стоит, между укладками
лучше подождать полчасика. Концы после обрезки можно подкрепить
суперклеем.
В обшивке ножом прорезал дыру, прикрутил ее к фанерному основанию
саморезами. В самой двери пришлось немного расширить штатное отверстие
под динамик. Для создания монолитной конструкции "подиум-дверь" из
фанеры 10мм вырезал подкладку, намазал герметиком и наглухо прикрутил
7-ю саморезами к двери. Когда прикладываю обшивку с привинченным
подиумом к двери, то она плотно прижимается к подкладке. Далее все это
стягивается саморезами по периметру внутреннего отверстия в основании
для образования монолитной конструкции.
В итоге цель была достигнута: подиум через подкладку намертво привинчен
к железу двери. Саму обшивку двери собираюсь крепить саморезами, но пока
она держится на штатных пистонах.
Вот вроде и все, остается добавить, что конструкция до конца не
завершена - нет динамиков... Остается лишь надеяться что они появятся в
недалеком будущем :-)
Установка динамиков
Динамики появились - ими оказались компонентные ???, Выяснилось, что
мидбасы не помещаются в подиумах - и корзина шире, и магнит значительно
больше ожидаемого. Поэтому посадочные места мне пришлось рассверливать,
причем в довольно грубой форме...
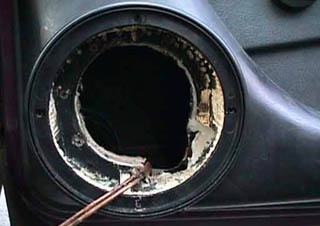
Все же внутреннее отверстие в подиуме оказалось
недостаточно широкое для такого массивного магнита. Да, такому мибдасу
нужно дышать, причем "во всю грудь" Но изменить конструкцию уже не
представлялось возможным...
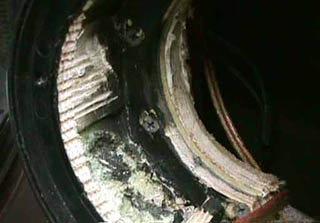
На снимке можно разглядеть крепление подиума
саморезами через прокладку к железной поверхности двери.
Пластиковую подкладку под динамик
я приклеил силиконовым герметиком к поверхности подиума, исключив тем
самым все неплотности прилегания.
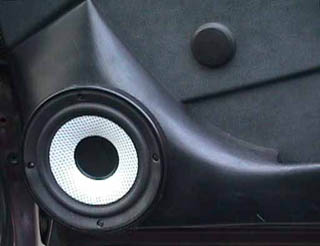
Вот итоговая конструкция с динамиком без снятой
защитной сеточки. Вроде неплохо, однако маловат все-таки подиум для
такой головки...
Мидбасы показали отличный звук -
глубокий и плотный бас. Конструктив подиумов, их крепление также отлично
себя показали. Хотя практика изготовления подиумов при наличии
отсутствия динамиков не может быть признана правильной - в моем случае
из-за малой величины внутреннего отверстия подиума наблюдался "туннельный
эффект". Это означает, что на большой громкости масса воздуха, двигаемая
диффузором, не успевает беспрепятственно перемещаться между магнитом
головки и внутренностями подиума. Таким образом за мембраной образуется
разряжение и динамик начинает "стучать катушкой", хотя запас по
электрической мощности еще не достигнут. Чтобы этого избежать, нужно
делать внутренние отверстия как можно шире.
Здесь я писал про ВАЗ-2109 и ВАЗ-2110, скоро надеюсь их продать и хочу
купить ВАЗ-2114, и многое к ней :-) . Я уже насмотрел себе эту машину в
сервисе цвет амулета.. но дальше думаю никому неинтересно, а кому
интересно могу написать как буду тюнинговать "четырнадцатую".
Источник:
http://www.sporttuning.ru
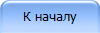
После смены магнитолы на более
приличную (читай: мощную) стала остро ощущаться нехватка мидбаса и
средних частот впереди. Стоявшие в передних дверях 10-см Sony явно не
были рассчитаны на мощность магнитолы. Это и стало последней каплей,
заставившей меня взяться за изготовление подиумов и установки нормальной
акустики в передние двери. В качестве неё были выбраны трёхполосные 'блины'
Bazooka EL690 размером 6x9''. От трёхкомпонентной акустики отказался
сразу по причине дороговизны, да и 'пищалки' уже стояли в передних
стойках, жалко было выбрасывать.
Итак, формирование звуковой сцены предполагалось осуществить при помощи
следующей схемы: трёхполосная акустика с отключенным твитером в нижней
части передней двери и ВЧ-излучатели, расположенные в стойках кузова
непосредственно у передней панели.
Мне очень не хотелось уродовать внутреннюю металлическую стенку двери,
поэтому расположение динамика и его ориентация были выбраны так, чтобы
магнит оказался над (или слегка заходил внутрь) штатным отверстием под
динамик (напомню, машина конца 1996-го года, место под динамик в двери
уже есть). За чёткостью сцены я не гнался, считая, что частичная её 'размытость'
вполне допустима в автомобиле. И тем не менее, после сборки всей системы
оказалось, что я почти не ошибся с углами :-)
Что потребовалось для работы:
картон для изготовления макетов (несколько коробок из-под материнских
плат),
10-мм фанера 1 кв. м. (50 руб), 3-мм фанера, 0.7 кв. м,
монтажная пена MicroFoam 500 г. или любая другая, MacroFlex и т.п. (77
руб.),
стеклоткань 0.25 мм 1 кв.м., (30 руб), эпоксидная смола 1.5 л и
отвердитель 0.1 л,
растворитель "650" 1 л,
шпатлевка "Тинейсик" со стекловолокном, 0.5 кг (75 руб. плюс шпатель
резиновый, 15 руб)
шурупы с потайной головкой 14 шт, саморезы с полукруглой большой
головкой (грибок) 15 мм и 20 мм, около 15 шт.,
искусственная кожа под цвет обшивки двери, 1 кв. м., 70 руб.
гвоздики 10 мм в количестве одного спичечного коробка, 5 руб.
Из инструментов понадобились электролобзик, электродрель и шлифёрка.
Отвёртки, ножи и прочие мелочи не учитываю :-)
Технология построения подиумов
оригинальностью не отличается: изготавливается силовой каркас из 10-мм
фанеры в виде основания, прилегающего к обшивке двери, и овала, на
котором будет 'сидеть' динамик. Для подгонки основания под рельеф
обшивки используются кусочки 3-мм фанеры (место около кармана). Овал
фиксируется на основании при помощи 3-х стоек (четвертая не нужна,
вместо неё выступает само основание), которые закрепляются при помощи
шурупов с потайной головкой. Будьте внимательны при выборе места для
стоек! Уменя шуруп, крепящий стойку, аккуратно попал под место для
крепления динамика. Далее на каркас напыляется монтажная пена,
выдерживается около суток и обрабатывается ножом и крупнозернистой
шкуркой до придания необходимой формы.

Следующим этапом
следует выведение поверхности под оклейку стеклотканью. Все ямки и
прочие погрешности аккуратно замазываются шпатлёвкой. После высыхания
излишки и неровности обрабатываются шлифёркой. Хочу обратить внимание на
строгость соблюдения соотношения отвердитель-шпатлёвка, при избытке
первого застывшую массу очень тяжело обрабатывать.
Далее очередь стеклоткани. Необходимо её отжечь на костре или паяльной
лампой перед началом работы так, чтобы не осталось и намёка на парафин.
Толщина стеклоткани не критична, более тонкая (0.25 мм и менее) лучше
ложится, но в большей степени повторяет неровности и требует большего
количества слоёв для жёсткости. Приготовив смесь из эпоксидной смолы и
отвердителя (соотношение 20:1) и разбавив до нужной консистенции
растворителем, сначала замочил стеклоткань, затем нанёс тонкий слой
смеси на подиумы и, положив стеклоткань, аккуратно разгладил её так,
чтобы не осталось никаких пузырьков, складок и т.п. Излишки подрезал
ножницами. При толщине 0.25 мм я положил 2 слоя. Все работы выполнялись
голыми руками, так что в остатках эпоксидки руки были ещё неделю после
окончания работ :-) Для отмывания рук и тары от смеси использовался
растворитель.
По истечении суток всё высохло, ножом с зубчатым краем вырезал отверстие
под динамик и проверил, как подиум ложится на обшивку двери. Все
появившиеся неточности ликвидировал шлифёркой.
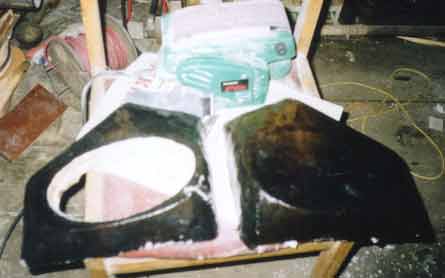
Далее предстояло обтянуть подиумы
искусственной кожей. Сапожное ремесло, как, впрочем, и все описанное
ранее, осваивал впервые, так что без небольших ошибок не обошлось. Кожу
следует натягивать так, чтобы на углах не появились складки. При этом
одна большая складка разбивается на множество маленьких, которые
аккуратно вытягиваются на внутреннюю часть "болванки", где и фиксируются
гвоздиками. Честно признаюсь, полностью без складок обтянуть не удалось,
их сделал в нижей части, скрытой от глаз. Кожу, находящуюся на овале
динамика, приклеил "Моментом", чтобы при вырезании овала она не
разъехалась. Для надёжности прихватил ещё и 4-мя гвоздиками, хотя это
лишнее.
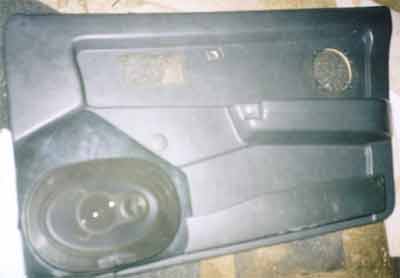
Внутреннюю подсветку
динамиков выполнил следующим образом: при помощи термоклея по всему
периметру обратной стороны динамика закрепил 8 лампочек в патронах,
изъятых из старой комбинации приборов, соединил их параллельно и вывел
отдельным разъёмом на подключение.
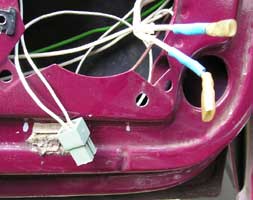
В обшивке двери вырезал овал под
динамик, по внутреннему периметру основания подиума нанёс слой герметика
и вместе с динамиком прикрутил саморезами к обшивке двери. Оказалось,
что магнит динамика практически не выпирает из обшивки, так что
издевательство над металлической частью двери я не проводил. Особое
внимание уделил карману, который пришлось подрезать. Для крепления его к
обшивке двери использовалось одно штатное место, а второе пришлось
делать самому в виде трех склеенных дихлорэтаном кусочков пластика,
наклеенных внутрь кармана. В результате карман держится, как и раньше.
Дошла очередь до звукоизоляции. Из 3-мм фанеры вырезаны элементы,
повторяющие отверстия в дверях, приклеены на герметик. На обратную
сторону обшивки положил лист поролона 8 мм, закрепив его штатными
клипсами-"ёлочками".
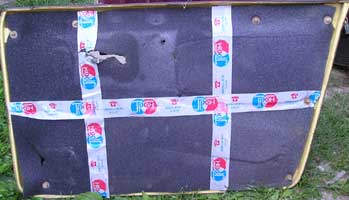
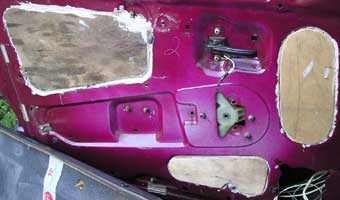
Протянул новые провода для динамиков,
провод для подсветки динамика и
ручки открывания двери. Через разъёмы "папа-мама" всё подсоединил и
поставил обшивку на место, закрыв отверстия от старых динамиков
декоративными вставками. Продаются они только комплектом, так что и
задние двери пришлось "облагородить".
На всё у меня ушло около трёх недель, правда, всё делалось в чужом
гараже и работать в день приходилось 2-2.5 часа. Результат - на фото.
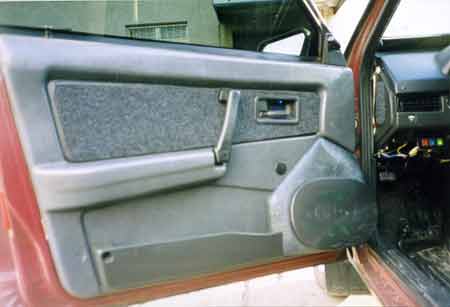
Ночью это творение выглядит достаточно
красиво:
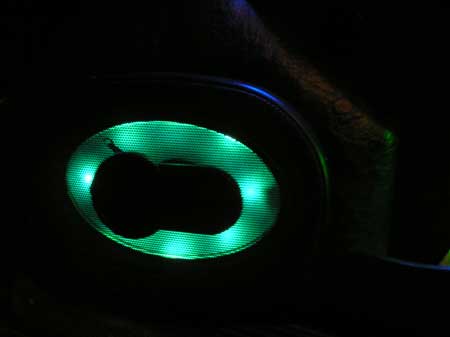
Недостатки всё же есть. Так как
отверстие под динамик не было вырезано в металлической части двери, на
громкости выше средней чувствуются искажения. Видимо, объём воздуха,
прокачиваемый динамиком, не успевает беспрепятственно проходить в
полость двери, создавая дополнительное сопротивление движению диффузора.
Так что полноценный мидбас, как показала практика, без вмешательства в
конструкцию двери сделать не удалось. Возможно, позже я исправлю этот
недостаток.
Ещё один заключается в сильной вибрации всех четырёх дверей на приличной
громкости, создающей на улице весьма громкое металлическое бряканье. Но
внутри этого не слышно. Шумоизоляция дверей не помешала бы...
Источник:
http://a080ac.nm.ru/
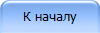
После изготовления
подиумов пришла очередь подумать о сабвуфере. Конечно, можно было бы
просто купить корпусной саб, но для меня это слишком легкий путь. Да и
вообще, если хотите знать мое мнение, готовый ящик для настоящего
мужчины должны делать только один раз, и совсем под другую музыку...
ВАЗ-2109 (ОПЫТ 1999-2000 г.)
Для начала я изучил
все статьи о теории и практике "сабостроения" на сайте журнала "АвтоЗвук",
включая опубликованные ещё до появления журнала на свет и не
опубликованные вовсе (это можно найти на сайте в разделе "Разное"),
просмотрел все, связанное с композитными материалами, и сделал свой
выбор. Обосновывать свой выбор головки для саба я не стану, тема
отдельная. Скажу только, что это 12 дюймовый MTX Thunder 5124.
Производитель рекомендовал закрытый ящик 1.25 cu.ft, а с учетом
характеристик зубильного салона, по расчетам выходило 34 литра (1.22
cu.ft). На чем я основывался.
Выбор технологии
Внимательно
ознакомившись со всеми рекомендациями, решил строить ящик типа "stealth"
(скрытый, неправильной формы, повторяющий форму части багажника) из
стеклоткани и углеволокна со стенками из фанеры.
Материалы и инструменты
Из основных
материалов мне понадобилось:
Эпоксидка, 9 флаконов по 300 г,
пр-во г. Дзержинск.
Стеклоткань толщиной 0,3 мм (скорее
всего, она промышленная), без воска, порядка 2,5 кв. м.
Углелента толщиной 0,1 мм и
шириной 0,4 м - порядка 4 м.
Лист фанеры 9 мм - порядка 1,8
кв. м.
Полиэфирная шпаклевка со
стекловолокном - 150 г.
А также шкурка, гвоздики, шурупы,
бумажный скотч, пластилин, аэрозольная краска "Matson", клей типа "Момент",
термоклей, карпет (ковролин).
Электролобзика у
меня тогда не было, поэтому использовал обычные пилы - широкую и узкую,
также электродрель, строительный фен "Black&Decker", ножницы по металлу,
нож-резак и еще молоток...
Выклейка
Решил расположить
сабвуфер слева в багажнике - меньше расстояние до аккумулятора и больше
места в нише из-за отсутствия горловины бензобака. Место, которое
находится за пластиковой заглушкой, тоже задумал использовать, и, как
потом оказалось, не зря, это дополнительно 5 литров объема. Для начала
подготовил поверхности: все заклеил бумажным скотчем, включая
пластиковую боковину. Затем с помощью картона, скотча и пластилина
сделал обечайку (торцы) вокруг выреза вровень с кромками, предварительно
наклеив кусок пенки 8 мм на внутреннюю поверхность заднего крыла. Это
для того, чтобы готовая форма не упиралась в крыло изнутри. Здесь важно
проследить, чтобы боковые картонные стенки располагались под небольшим
углом, иначе слепок невозможно будет вытащить из отверстия. Потом тем же
пластилином немного подкорректировал получившуюся матрицу для придания
более плавных обводов слепку. Пластилин разогревал феном, а то очень
тяжело.
Подготовленную таким
образом поверхность обильно смазал литолом и приступил к оклейке.
Стеклоткань накладывал внахлест, полосками шириной порядка 15 см, слегка
подогревая их феном и выдавливая пузырьки. Поверхность смолой не мазал (она
в литоле), а предварительно пропитывал полоски. На этом этапе я не очень
ясно представлял себе будущую форму ящика, поэтому заклеил заведомо
большую площадь.
Эпоксидка медленно
полимеризуется при низких температурах, поэтому мне пришлось искать
теплый гараж для затвердевания формы. Это оказалось гораздо легче, чем я
предполагал, и после ночевки машины в огромном теплом заводском гараже я
торжественно выдрал получившийся слепок, правда, с некоторым усилием...
Стенки
Число, форму и
размер боковых стенок прикидывал уже по месту, вырезая их из картона и
скрепляя клеем-расплавом (продается в виде стержней, плавится паяльником
либо вставляется в специальный "пистолет"). Но на этом этапе есть одна
важная проблема, для которой я нашел (горжусь собой!) нетривиальное
решение.
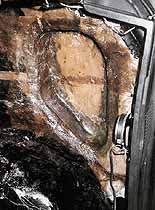
Не удалось
сфотографировать форму перед оклейкой. Стеклоткань положена в один слой
внахлест, сквозь нее виден бумажный скотч и пластилин
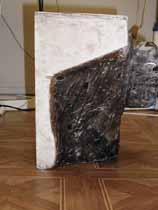
Слепок отлично
приклеился к деревянной стенке на самом неровном участке. Если
приглядеться, то по периметру заметны следы от гвоздиков
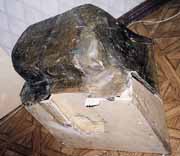
Этот вырез под
штатный динамик "тыловой подзвучки". Использована та же фанера 9 мм,
эпоксидка и маленькие гвоздики
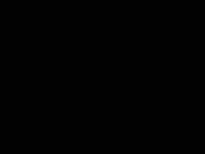
Верхняя стенка.
Вырез под динамик не имеет второго слоя фанеры, но потом я наклеил на
него ребро жесткости
Как прикинуть объем ящика? Готового
ответа я так и не нашел, пришлось придумывать. Коробка от динамика
вмещала 20 литров, поэтому на глазок вырезал из картона и скрепил стенки
так, чтобы получилось полторы коробки. Более точно измерить объем можно
только при помощи сыпучих или жидких веществ... Может подойти и крупа
(30 литров крупы - ой-ой!), песок, керамзит или пенопластовые шарики...
Про воду пока речь не идет - конструкция негерметична в принципе. Но
свежее решение пришло само собой, однако не сразу: в обычные пакеты для
мусора я налил воды по 6 литров, завязал их и просто побросал в макет
ящика! Хотя конструкция чуть было не рассыпалась из-за тяжести воды,
цели своей я достиг...
Затем вырезал стенки
уже из 9-миллиметровой фанеры, стараясь учесть уменьшения объема в
дальнейшем: толщина стенок, объем брусков и ребер жесткости, эпоксидку
(9 флаконов по 300 г), стеклоткань и т.д. Новые стенки скрепил
термоклеем и вторично произвел замер. Если есть сомнения в правильности
замеров, то можно ширину стенок сделать с запасом и отрезать лишнее
потом, когда будет набрана достаточная прочность. Верхнюю стенку
пришлось вделать с вырезом под динамик в штатном месте накладки. Так я
планирую организовать тыловую подзвучку.
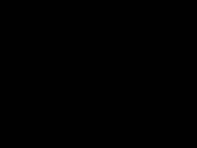
Днище и часть задней
стенки поклеены одним куском. Видно, что в "сэндвиче" слои углеленты
более узкие, чем стеклоткань по краям. Пока набрана лищь половина
толщины
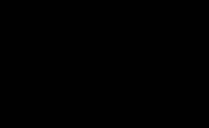
Саморезы расположены несколько хитро - чтобы они не "встретились" внутри
бруска. Для лучшего утапливания головок место предварительно рассверлил
большим сверлом
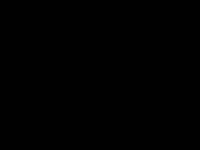
Прямо по курсу - стенка, прилегающая к арке колеса. Ее пришлось
усиливать, плюс еще и ребро жесткости
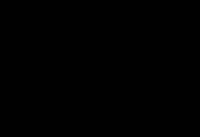
Деревянная обвязка в один слой, дно еще не приклеено основательно.
Слепок изнутри пришлось немного подшлифовать
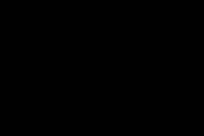
Ящик и верхняя крышка готовы к соединению. По краю стенок приклеил
полоски фанеры - немного увеличил ширину стенок и, соответственно, объем
ящика Далее
скреплял стенки между собой при помощи шурупов (саморезов), брусочков и
эпоксидки. Бруски лучше вырезать из твердых пород дерева: бук, дуб,
береза. Места под шурупы (я взял 4 х
25 мм) разметил и предварительно
засверлил сверлом 0,5-0,75 диаметра шурупа, иначе брусок расколется.
Хочу добавить, что скреплял боковые стенки между собой, не отделяя
заднюю, - чтобы постоянно контролировать положение деревянной части
относительно стеклопластиковой. То есть разрывал временное клеевое
соединение, ставил брусок и опять фиксировал участок термоклеем. Когда
деревянная обвязка высохла, капитально приклеил к ней заднюю стенку
эпоксидкой, прибив штапичными (маленькие такие) гвоздиками по периметру
для полного прилегания. После этого срезал излишки слепка и кое-где эти
гвоздики повыдергал. При стыковке все щели заполнял смесью смолы и
опилок. Первоначальная форма была готова. Даже на этом этапе ящик
оказался полностью герметичным, поэтому я замерил объем водой, причем
уже без пакетов...
Увеличение прочности
Для увеличения жесткости деревянных стенок достаточно было просто
прибить-наклеить еще один слой фанеры. Но я на свой страх и риск немного
усложнил себе задачу и применил композитный материал - "сэндвич". Между
двумя фанерными стенками зажал три слоя углеволокна со смолой, причем
волокна располагались вдоль - поперек - вдоль. Дополнительную стенку
решил высверлить и сделать, таким
образом, "сотовую" структуру. Как мне кажется, эти дырки не снижают
общую жесткость конструкции, но заметно улучшают демпфирование стенок.
Да и к тому же в сумме это дополнительных 2 литра объема, я посчитал.
Вполне возможно, что эти дырки - спорный вопрос. Здесь я не уверен на
100% в правильности своих действий, однако испытания показали неплохие
результаты...
Другое дело - набрать
прочность стеклопластиковой части ящика. Оптимальным решением оказалось
применение аналогичного "сэндвича". Только теперь три-четыре слоя
углеволокна помещались между слоями стеклоткани. Такой "сэндвич" я
аккуратно изготавливал на гладкой подложке (идеально - на куске толстого
стекла), тщательно пропитывая смолой каждый слой. Потом наклеивал его
внутрь слепка. Предварительно поверхность смазывал эпоксидкой и уже
положенный "сэндвич" немного грел феном (смола размягчалась), тщательно
разравнивал его, выдавливая пузыри, и затем грел феном уже посильнее.
После таких действий свежеприлепленный "сэндвич" "вставал" - немного
затвердевал. Таким образом, вполне возможно набрать жесткость слой за
слоем, не дожидаясь полной полимеризации свежих "сэндвичей".
По такой схеме набрал
суммарную толщину в 8-10 слоев, накладывая куски внахлест и делая акцент
на участках с наибольшей площадью. Также старался, чтобы "сэндвич"
немного захватывал фанерные стенки. Форма выклеивалась довольно ровно,
поэтому поверхность практически не шлифовал между накладкой слоев.
Углеволокно имеет высокий модуль жесткости, поэтому его применение
намного упрощает задачу. Можно, конечно, обойтись и без него, но тогда
число слоев стеклоткани придется увеличить... И еще один момент:
композит получится гораздо прочнее, если он будет сохнуть под грузом, а
не просто так. Вакуумной установки у меня нет, применять гнёт я не стал,
но прижать стеклоткань мешочком с песком, наверное, было бы не лишним...
Ребра жесткости и верхняя крышка
Конструкция
получалась все прочнее и прочнее. Я пробовал со всей силы прыгать на
ящике, но никаких деформаций это не произвело. Тем не менее, поставил
ребра жесткости (распорки). Прыжки прыжками, а бас - дело серьезное.
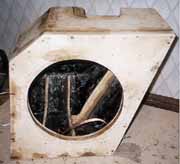
На фото часть отверстий зашпаклевана, но еще не зашкурена. Внутри ящика
видны ребра жесткости и провод к динамику
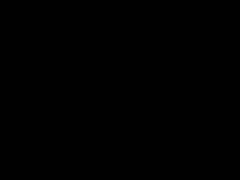
Вид сзади. Этот аппендикс вставляется в дырку в крыле внутри багажника.
Покрашено аэрозолью в полтора слоя. Внизу слева видны два столбика - это
клеммы
Ребер вырезал три
штуки - из той же фанеры, шириной 3-4 см. Конечно, не так просто было "близко
к тексту" повторить рельеф стеклопластиковой поверхности, но я особо и
не старался: стеклопластик все спишет... Ребра наживил гвоздиками к
деревянным стенкам, заполнил щели между ними и слепком смесью смолы и
опилок, а потом по месту стыка положил полоски стеклоткани. На дно ниши
приклеил буковый брусочек, заклеив его сверху куском стеклоткани. Ну вот
теперь прочность точно достигла отметки "ЛИНКОР".
Верхнюю крышку тоже
вырезал из фанеры. Между двумя 9-миллиметровыми заготовками зажал пару
слоев углеволокна и слой стеклоткани со смолой, скрепил фанерки
гвоздиками и прижал грузом. Отверстие под динамик вырезал заранее, а уже
к высохшей композитной конструкции приклеил и прибил дополнительное
кольцо. Оно немного добавляет жесткости крышке, да и шурупы крепления
динамика будут прочнее держаться за счет более долгого пути в дереве...
После проверки
поверхностей крышку торжественно приклеил к ящику, намертво привинтив ее
шурупами. Мелкие неровности и головки шурупов зашпаклевал и зашкурил.
Стеклопластиковую часть ящика тоже шпаклевал, но только крупные раковины
- выводить поверхность "в ноль" не имеет никакого смысла: кто это оценит,
а на жесткость не влияет.
Ящик снаружи и
изнутри выкрасил черной матовой краской, хотя специалисты рекомендуют
внутреннее пространство обработать антикором в аэрозольной упаковке.
Также изнутри на клей "Момент" наклеил 10-миллиметровый поролон для
лучшего демпфирования стенок. Снаружи часть ящика задрапировал
ковролином (карпетом), использовав тот же "Момент".
Клеммы купил
универсальные - и под вилку, и просто под оголенный провод. Просверлил
отверстия в боковой стенке и прикрутил их, промазав герметиком. Провод к
динамику взял покороче и потолще, 4 кв. мм, места контактов пропаял и
заизолировал.
Герметизация динамика
Неправильное
сопряжение динамической головки и ящика (особенно это касается ЗЯ)
запросто может свести к нулю весь кропотливый труд. Конечно, существуют
специальные прокладки из пористого материала, предназначенные специально
для подкладывания под обод динамика. Можно даже приклеить динамик к
корпусу герметиком. Но как его потом отдирать? Я применил простую и
надежную технологию, дающую прекрасные результаты. Всем рекомендую.
Обод корзины динамика намазал (от греха) литолом. Затем нанес
силиконовый герметик (отличные результаты дает фирменный "ABRO") по краю
отверстия в корпусе. Чтобы головка не приклеилась, по силиконовой
дорожке нужно уложить полоски тоненького целлофана (вполне подойдут
кусочки пакета - "маечки"). Далее нужно приложить динамик, ориентировав
его так, как он будет стоять в дальнейшем, и привинтить его всеми
винтами. После затвердевания герметика динамик и целлофан должны с
легкостью отсоединиться, а на корпусе должна остаться идеально
подходящая под конкретную головку силиконовая прокладка.
Выводы
На мой взгляд, сабвуфер получился. Не
особо тяжелый, но жесткий и прочный. В итоге он оказался около 33 литров
- ненамного меньше расчетного, но это не столь страшно: добавление
звукопоглощающего материала внутрь позволяет исправить эту нестыковку...
В багажнике сидит как влитой, не дребезжит, стенки не "дышат" даже на
околомаксимальной громкости. В общем, я доволен. В тот момент у меня нет
возможности измерить АЧХ, поэтому настраивал на слух - добавляя или
убирая акустический балласт или звукопоглотитель.
15 апреля 2000 года
появилась возможность проверить сабвуфер в деле на первых соревнованиях
SPL-клуба. Для меня оказалось полной неожиданностью, но сабвуфер в
категории "СОЛО" продемонстрировал звуковое давление в 132,5 дБ - лучший
результат среди всех участников. Для одной "двенашки" это очень серьезно.
Источник: Журнал "АвтоЗвук" 2002
#5, Дмитрий Цыпченко.
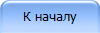
Об этом я мечтал давно.
Только представить: открываю багажник, а там - чистота, красота, порядок,
масса свободного места и, главное, ни одного болтающего провода. В
идеале - вообще не видно проводов! В предыдущей машине реализовать свою
мечту мне так и не удалось. Максимум, на что меня хватило, прикрутить
усилитель на фанерной подставке к спинке заднего сиденья. Однако в
текущей машине решил кардинальным образом исправить ситуацию. Но как?
Стоит ли говорить, что различных инсталляций я насмотрелся предостаточно.
Однако спроецировать что-нибудь из увиденного на свой багажник как-то не
получалось, ничего не нравилось... Нужна была оригинальная идея, причем
конструкция должна была бы отвечать определенным требованиям:
Провод питания аппарата должен иметь наименьшую длину;
Усилитель и провода не должно быть видно (вариант скрытой установки);
Моментальный доступ к регулировкам и клеммам, никаких проблем с
коммутацией проводов;
Конструкция должна занимать минимум места в багажнике и обеспечивать
нормальное охлаждение усилителя;
При всем этом решение должно быть простым и изящным.
Схема с креплением усилителя под передним сиденьем мне совсем
неинтересна. Спинка заднего сиденья тоже сразу отпала: было уже,
проходили - при откидывании спинки аппарат будет мешаться, да и к блоку
регулировок тянуться далековато. Поэтому для выполнения первого и
третьего требований решил установить конструкцию в левой части багажника;
силовой провод от аккумулятора у меня проложен по левой стороне кузова,
практически по прямой, так что первое условие выполнялось. Подходящим
местом оказалось только пространство возле арки левого заднего колеса, в
котором я решил расположить откидывающуюся конструкцию в виде
перевернутой буквы "Т" с усилителем, закрепленным "лицом к стене".
Инструменты и материалы
Из материалов мне потребовалось:
Обрезки десятимиллиметровой березовой влагостойкой мебельной фанеры
площадью не более 0,5 кв. м.;
Полфлакона Дзержинской эпоксидки;
Грамм 30 полиэфирной шпаклевки "Body" со стекловолокном;
Штук 10 черных саморезов длиной 70 мм, немного оцинкованных гвоздей
35х2;
Отрезок мебельной петли не более 50 см длиной:
Грунтовка и черная краска "Maston" в аэрозоле;
Отрез тянущегося карпета 0,5*2м, на вид либо "А21 Charcoal", либо " А23
Heater Charcoal". К нему специальный полиуретановый клей в аэрозольной
упаковке "Bondo" Spray Adhesive.
Набор электроинструментов стал уже стандартным - электролобзик "Skill",
электродрель "Sparky" с насадкой для шлифования, круги зернистости 30 и
80. Плюс такой же стандартный набор ручного инструмента.
Каркас
Из фанеры вырезал основание конструкции в форме, очень похожей на
боковой "лепесток" покрытия пола багажника, которым прикрыты глубокие
ниши возле арок колес. Подогнал форму таким образом, чтобы она, будучи
прикрепленной длинной петлей к полу, свободно накрывала нишу, а также
беспрепятственно поднималась на 90 градусов.
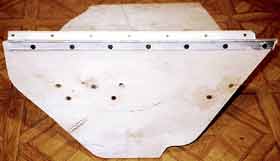
Основание полки. Туннель для проводов еще не прорезан, но петля уже
прикручена. Также видны следы саморезов, крепящих подставку.
Своим правым краем основание должно опираться на выступ арки колеса.
Прикинув глубину установки аппарата,
вырезал из двойной фанеры фигуру, к которой и должен крепиться усилитель.
Форму подставки пришлось подгонять так, чтобы она как можно более точно
повторяла обводы выемки. В итоге подставка своими краями плотно "усаживается"
в ковровое покрытие арки колеса без образования щелей. Второй,
внутренний слой фанеры имеет вырез в центре в виде арки - при склеивании
слоев образуется выемка под усилителем, в которой я планировал подводить
межблочные кабели.
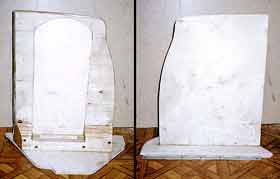
На левой части отчетливо виден вырез в виде дверного проема с аркой :-)
Конструкция в виде буквы "Т" успешно
получалась, но для надежного соединения ее частей требовалось что-то еще.
Кусочками фанеры нарастил нижнюю часть подставки, сделав в ней вырезы
под клеммы усилителя. Причем в двух средних слоях наборного брусочка
убрал центральную часть, оставив только края - таким образом образовался
"туннель" для проводов. Такой же туннель пришлось проделать и в
основании полки, чтобы все коммуникации можно было бы незаметно подвести
к усилителю под фальшполом багажника и ковровым покрытием арки колеса.
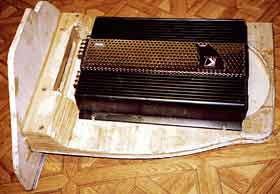
Вот так будет располагаться усилитель.
Все провода должны подводиться через "туннель" - питание и акустические
подключатся к клеммам, а межблочники пройдут под усилком и
присоединяться с противоположного торца. Хорошо
видна форма наборного бруска: выемка под клеммы усилителя и туннель для
проводов.
Как и в случае с сабвуфером, все
фанерные части я вырезал элекролобзиком, тут же скреплял их гвоздями и
подгонял электродрелью с шлифовальным кругом. Затем все деревянные части
склеил воедино эпоксидкой, прихватив наиболее ответственные места
саморезами. Петлю намазал "жидкими гвоздями" и привинтил к основанию
саморезами.
Отделка
Поверхности слегка зашкурил и подшпаклевал, покрыл грунтовкой (скорее за
компанию с сабвуфером). Так как в основном вся поверхность планировалась
под оклейку карпетом, то основательно выкрасил черной краской только
выемку под межблочники, а все остальное покрыл в один слой на всякий
случай.
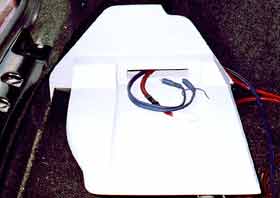
Вот так должна
откидываться конструкция, крепление к полу багажника соответствует
действительности.
Для наглядности в туннель просунуты провода.
Покрашенную полку еще раз примерил по
месту в багажнике и потом почти целиком оклеил ее карпетом, за
исключением обратной стороны основания и области под усилителем. К
готовой конструкции прикрепил усилитель, привинтил петлю к полу
багажника саморезами и подсоединил провода. Получилось просто
замечательно!
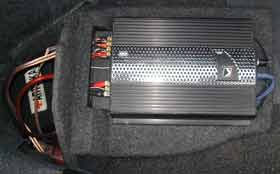
Полка полностью откинута. Видно, что ниша полностью функциональна -
наличие в ней аптечки это доказывает.
Провода пока не уложены и болтаются как попало, я буду их менять и
упорядочивать. Позже...
Были опасения - а как фиксировать полку
в закрытом состоянии, не будет ли она самопроизвольно открываться на
крутых виражах? Но раньше времени не стал усложнять себе задачу, и, как
впоследствии оказалось, правильно. Во-первых, усилитель смещен в нужную
сторону относительно оси вращения (откидывания), за счет этого он своим
весом как бы "закрывает" дверцу. Во-вторых, оклеенная карпетом подставка
достаточно плотно усаживается в коврик багажника. Таким образом за пару
недель поездок "дверца" ни разу несанкционированно не открылась... В
крайнем случае пара полосок "липучки" на торцах дадут 100%-ную гарантию
неподвижности конструкции.
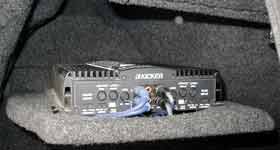
Полка приоткрыта градусов на 30. И вот они, все регулировки!
Удобство просто не описать словами, крути - не хочу !
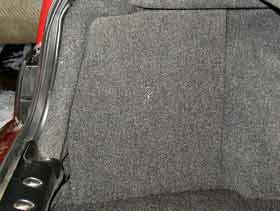
Как и задумывалось - не видно ни усилителя, но одного провода! Даже не
верится, что радость была так близка и доступна :-) Все, с такой
красотой прямая дорога на соревнования.
Как и задумывалось - не видно ни
усилителя, но одного провода! Даже не верится, что радость была так
близка и доступна :-) Все, с такой красотой прямая дорога на
соревнования.
Коврик пола багажника пришлось немного подрезать, но без этого - никак.
И на этом этапе вмешательство во внутреннее пространство багажника я
закончил.
Выводы
Я очень доволен получившейся конструкцией, особенно соотношением
трудозатрат к достигнутому эффекту. Действительно, валяющийся в
багажнике усилитель (прикрученный к спинке) создавал сильный дискомфорт,
который даже умудрялся проникать в салон :-) Полка отвечает всем
обозначенным выше требованиям, включая охлаждение усилителя. Карпет
обивки настолько совпадает с "родным", что в полумраке багажника на
первый взгляд вообще ничего лишнего не заметно. Осталась лишь проблема
нормального освещения багажника, которая в инсталляции играет далеко не
последнюю роль...
Вырезал я полку моментально, по сравнению с трудозатратами на новый
сабвуфер это просто ерунда, всего лишь пара взмахов электролобзиком.
Обтяжка карпетом в целом удалась, правда, пришлось наклеить пару
тренировочных кусочков. Со звуком (шумы, наводки, фон) никаких проблем,
чего я тоже немного побаивался. Но почти все провода я буду менять и
укладывать заново, хотя будет это ближе к теплу, как предполагается...
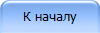
|